合成塑料前体,如聚合物,需要专门的催化剂。然而,传统的以批量为基础的方法寻找和筛选特定结果的正确方法需要消耗大量的溶剂,产生大量的化学废物,而且是一个昂贵、耗时的过程,涉及多次试验。
纽约大学坦顿工程学院化学和生物分子工程学教授瑞恩·哈特曼和他的实验室开发了一种基于实验室的“智能微系统”,该系统采用机器学习技术,用于模拟化学反应,有望消除这一昂贵的过程,并最大限度地减少对环境的危害。
在他们的研究中,“将自动化微流控实验与机器学习相结合,实现高效聚合设计”发表在《自然机器智能》杂志上,合作者,包括博士生本杰明·里兹金,使用了一种定制设计的,快速原型微反应器结合自动化和原位红外热成像技术来研究放热聚合反应,众所周知,当有限的实验动力学数据可用时,这种反应很难控制。通过将高效微流控技术与机器学习算法相结合,以获得基于最小迭代的高保真数据集,他们能够将化学废物减少两个数量级,并将催化发现的时间从几周减少到几小时。
哈特曼解释说,设计微流体装置需要团队首先估计聚合反应的热力学,在这种情况下涉及一类茂金属催化剂,广泛用于聚乙烯和其他热塑性聚合物的工业规模聚合。“我们首先对热量和质量的传递进行了数量级的估计。“对这些量的了解使我们能够设计一种微流体装置,它可以筛选催化剂的活性,并提供可扩展的机制,模拟工业规模过程所需的内在动力学。”
哈特曼补充说,这样一个台式系统可以为一系列其他实验数据打开大门。他解释说:“它可以为分析其他有趣的性质提供背景,例如流混合、分散、传热、传质和反应动力学如何影响聚合物特性。”
使用一类zirconocene-based聚合物催化剂,研究团队在研究其他成对microfluidicsproven放热reactionswith自动泵和红外热成像来检测基于温升的变化反应释放在他们生成热(化合物)导致高效、高速实验绘制催化剂的反应空间。由于该过程是在一个小型反应器中进行的,他们能够将催化剂溶解在液体中,从而消除了在极端条件下进行催化的需要。
“事实上,大多数塑料都是用与二氧化硅颗粒结合的茂金属催化剂制成的,这样就形成了一种异质底物,可以聚合丙烯和乙烯等单体。”“溶解茂金属的均相催化剂的最新进展使得反应条件更加温和。”
哈特曼的团队之前证明了人工神经网络(ANN)可以作为建模和理解聚合途径的工具。在新的研究中,他们将氮化碳纳米管应用于锆辛烯催化的放热聚合的建模。利用MATLAB和LabVIEW系统对反应进行控制,与外部设备交互,生成高级计算算法,根据实验结果生成一系列的神经网络来建模和优化催化。
化学公司通常使用100毫升到10升的反应堆来筛选数百种催化剂,而这些催化剂反过来又可以扩大到生产塑料。这里我们用不到1毫升,通过减少实验室实验的足迹,你减少了所需的设施,所以整个足迹减少了。我们的工作为复杂催化聚合的科学和技术经济分析提供了一个有用的工具,”哈特曼说。
哈特曼和他的实验室的发现为新类型的研究打开了大门,主要涉及自动化的概念,或“机器人”化学,提高产量,数据保真度,和安全处理高度放热聚合。他解释说,原则上,这种方法可以导致更高效的设计和更环保的塑料,因为筛选催化剂和聚合物的速度更快,可以更快地调整工艺,使之适用于更环保的聚合物。
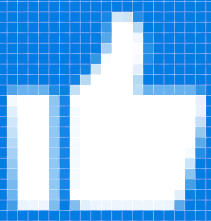